FAQs
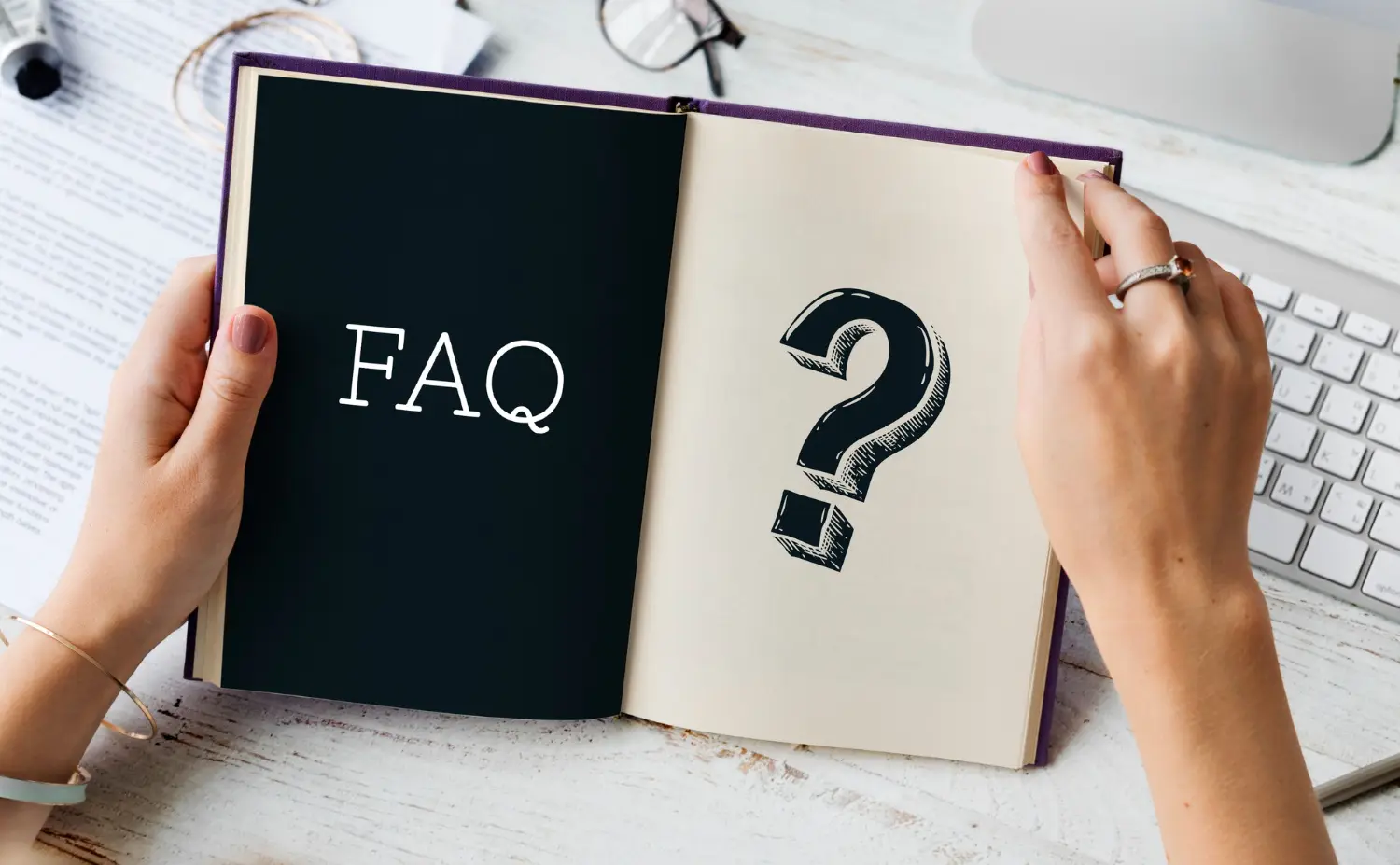
What is powder particle size, and why is it important?
Particle size refers to the average diameter of individual particles in a powdered material. In industries such as construction and manufacturing, particle size is an important factor as it affects a material’s physical properties, including flowability, surface area and reactivity. Smaller particles generally provide a higher surface area which can enhance binding in cement or improve reactivity in chemical applications.
What does mesh size mean in powder measurement?
Mesh size is a measure of the size of particles in a powder based on the number of openings in a screen or sieve per inch. For instance, a 200-mesh powder means it has passed through a screen with 200 openings per inch, resulting in finer particles compared to, say, a 50-mesh powder. Mesh size is critical in industries where uniform particle size is essential for consistent product quality.
How is micron size different from mesh size?
While mesh size indicates how finely a material is sieved, micron size gives a more precise measurement of particle diameter, often using tools like laser diffraction. One micron is one-millionth of a meter. While mesh is based on screen openings, micron size precisely measures particle diameter, giving a more exact sense of a material’s fine or coarse nature.
How are particle sizes converted from mesh to microns?
Conversion charts are used to approximate mesh size in microns since different screens capture varying particle shapes and sizes. For instance, a 325-mesh sieve typically filters particles around 44 microns. These conversions aren’t always exact, as particles vary in shape and can clog screens, altering results.
What methods are used to measure particle size in microns
Common methods include laser diffraction, sieving, and image analysis. Laser diffraction is highly accurate and quickly provides a full particle size distribution by analyzing how laser light scatters through the particles. Sieving works well for larger particles, and optical image analysis can capture individual particle shapes and sizes.
What is whiteness in materials, and why is it important?
Whiteness measures a material’s brightness and purity, with a high whiteness index often preferred in industries like plastics, paints, and coatings. Whiteness is important because it affects the visual appeal and quality of products where appearance matters, such as in decorative or construction applications.
How is whiteness measured in powders like calcium carbonate?
Whiteness is usually measured with the help of a spectrophotometer or colorimeter that shines light on the sample and measures the reflected light from it. Accordingly, a whiteness index value is obtained, where more increase in value indicates purer and more reflective materials. In construction, high whiteness materials such as calcium carbonate are used to give uniformity to the structural appearance.
It is in spectrophotometry and colorimetry that whiteness usually measures, with the sample receiving light and reflecting back, which also produces a whiteness index value, more increased values indicating pure and highly reflective materials. In construction, high-whiteness materials like calcium carbonate are most preferred for purposes of uniformity and aesthetics.
What is the difference between whiteness and brightness in powder measurement?
Whiteness assesses the balance of light across the visible spectrum, while brightness specifically measures reflection in certain wavelengths (usually blue). While both are measures of light reflection, whiteness covers more dimensions of color, making it a broader metric for aesthetic applications.
What is fineness in the context of cement and powders?
Fineness is normally describing the particle size distribution in powders and cement, significantly impacting reactivity and surface area of the powder. In cement, fineness is crucial since smaller particles react more readily with water, enhancing the hardening process and improving structural strength.
How is fineness measured in materials like cement?
Blaine air permeability method is often a fine measurement. It measures the amount of air that passes through compacted powder cement. A higher fineness value indicates smaller particles, favorable in those applications requiring quick setting and high initial strength. Consistent fineness has its importance in quality and workability during construction.
What is compressive strength, and why is it important in construction materials?
Compressive strength measures a material’s ability to bear loads without breaking. For cement and concrete, it indicates durability and suitability for structural applications. High compressive strength is essential in projects requiring long-lasting, load-bearing structures which plays very important role in construction and buildings.
How is compressive strength tested in cement?
There is a mortar cube that is cast for compressive strength testing, cured under specified conditions, and given pressure until it ruptures. The rupture point of the mortar cube is then recorded in megapascals (MPa), indicating the strength of the material. This official method has ensured that strength values would be comparable and consistent throughout the procedure.
What are cement grades in terms of compressive strength and how do they differ?
Now, the cement grades are classified on the basis of compressive strength after 28 days, which are measured in megapascals (MPa). The grades are 33, 43, and 53 grades which have the respective compressive strengths of 33 MPa, 43 MPa, and 53 MPa. Generally, lower grades, such as 33 MPa, cannot be used for structural purposes and are recommended for plastering and masonry works. However, a lot of the people prefer 43 grade cement for general construction purposes such as those concerning residential buildings and reinforced concrete constructions.
How is durability tested in building materials?
Durability testing assesses a material with respect to its endurance against weathering, wear and chemical action-including tests like freeze-thaw cycles, water absorption, acid and salt resistance. Ultimately, these tests qualify a material for durability in terms of structural integrity over time and long performance life.
What is thermal conductivity, and why is it important in construction materials?
Thermal conductivity measures a material’s ability to conduct heat. Materials with low thermal conductivity, like certain concretes, act as insulators, which helps in energy efficiency for buildings by reducing heating and cooling costs. Testing thermal properties is particularly important for materials used in walls, roofs, and flooring.
How is moisture content measured in building materials?
The moisture content of building materials can be defined as the moisture contents determined by the oven drying, moisture meters, or even how it is called, the gravimetric method. Within this methodology, a sample is weighed before and after drying in an oven at standard temperature, and thus, moisture content is indicated by weight difference. The moisture meters, including moisture pin and pinless forms, quickly measure moisture by the electrical resistance or electromagnetic signals principles. Accurate measurement of moisture is crucial to ensure the durability of structures, prevent structural problems, and maintain the quality of construction.